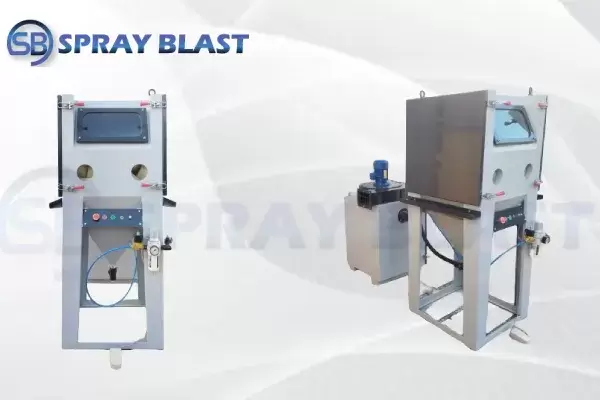
Abrasive grit blasting, also known as sand blasting. Grit Blasting Machine is a surface treatment process whereby abrasive particles are fired through a nozzle utilizing compressed air. Grit blasting is widely utilized in a variety of industries to clean or modify the surface properties of components.
Particles range from walnut shells (relatively soft), through different sands, to silicon carbide, alumina or emery particles, depending on the application.
Methods of propelling the particles also vary and involve entrainment in compressed air, liquid (usual water) or vapor (usually steam) streams, and mechanical projection methods (e.g. rotating paddles).
Grit blasting is utilized to remove sand and scale in the fettling of castings, and for the dressing of stampings and billets, etc. It is often used to prepare surfaces before welding (removal of scale, rust, or paint), and afterward to improve the adhesion of coatings (e.g. paint, or galvanizing).
Portable grit blasting machines use abrasive materials like sand (in the case of sand blasting machine equipment) to remove contaminants from the surface of parts. This is accomplished by spraying the parts with abrasive materials at very high pressures to remove dirt, rust, and another build-up. The result is a cleaner, stronger part that can be restored to work or look as it was originally intended. Grit blasting machines are particularly helpful in the automotive restoration industry where they are used to clean parts after a car has been disassembled.
Once the parts have been blasted, they can be painted and can be restored to its original appearance. Unlike when a part is sanded manually, a grit blaster will get into every crack and crevice because the particles of most abrasive materials are so small. This process results in a more thorough and effective cleaning and surface finish.
There are several types of grit blasting machines and each one is optimal for a particular industrial or commercial application.
1. A grit blasting cabinet is used in shop applications where parts need to be treated without creating dust in the surrounding area. The part is inserted into the cabinet which is then sealed before the pressurized abrasive material is forced through nozzles into the chamber. The operator can turn the machine on and off utilizing a foot pedal, and rubber glove hand inserts allow them to pick the object up and move it around as it is being blasted.
2. A grit blasting room works in much the same way as a blasting cabinet, except it is much larger and the operator actually works inside the room while wearing heavy protective equipment.
3. Other types of grit blasting machines or portable grit blasting machines utilize hydro-blasting, wheel-blasting, dry-ice blasting, and automated blasting.
Hydro-blasting, for example, utilizes highly pressurized water to blast surfaces like the exterior walls of buildings. Dry-ice blasting uses air and dry-ice under pressure that is ejected from a nozzle. This effectively removes surface contaminants due to the force of the carbon dioxide.
Grit blasting is an efficient way to harness the abrasive qualities of the material to thoroughly clean an industrial or commercial component. The different styles and sizes of grit blasting machines that are available make abrasive blasting an excellent solution for companies in many different manufacturing and repair industries.
Portable grit blasting machines manufacturer in India - We are leading manufacturer of grit blasting machines, portable grit blasting machine, grit blasting cabinet, bench top sand blasting machine, manual grit blasting machine, portable shot blasting machines Portable sand blasting machine, dust collector, abrasive hopper, Shot blasting machines, shot blasting cabinets, shot blasting Room, equipment in India. The grit blasting machines manufacturer, price is low and quality. Our aim is to satisfy the consumer.