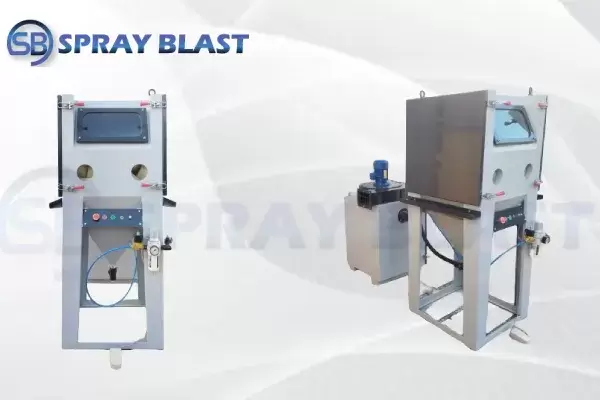
A grit blasting room is an important segment of the industrial coatings business. It is required to clean raw-off-the-mill and manufactured steel before applying a protective coating. In most cases, a shape is applied to the surface to give a key for the paint film to adhere properly. The concept of producing a grit blasting machine operation of high velocity abrasive at any object grew from the days when anyone who had a compressor & some kind of pressure vessel could direct some form of abrasive at work, however, abrasive was not recoverable. Using a grit blast room changes this equation, primary explanation that an individual establishes a blast room is to be capable of recovering & recycling their abrasive. This stops the process from becoming too costly & wasteful.
In a grit blast room, dust can be regulated by reasonable ventilation; good lighting permits the operator to see clearly, producing a consistent outcome quality, and where abrasive blasting machine operation could be accomplished 365 days a year without existing interrupted by climate situations, dew, etc. Like with an unconditional minimum of manual labor.
To maintain high productivity & minimum maintenance, grit blasting rooms must be properly built. Walls should be assembled of a 5mm steel plate that has been properly strengthened to avoid buckling. To reduce dust & abrasion, all internal exteriors should be devoid of protrusions within chamber. Lighting is critical in providing enough vision levels for the operator to view within angles, corners, cleats, & complicated manufactured components. Lights should not be installed within a grit blast room. To make the most of the chamber's space, the doors should be left open to give complete access. Floor grating & accompanying mounting systems should be designed to withstand the relevant loading levels. Typically, 50-ton loads are readily accommodated.
Installing a blast chamber has various advantages, both economically & environmentally. Weather limitations are no longer an issue. You may blast constantly 24 hours a day for a year, helping you to improve productivity & meet customer deadlines. The regulated atmosphere helps your blaster provide consistent results. Grit blasting rooms frequently have an automated abrasive blasting media recycling system, which permits you to utilize recyclable abrasives while significantly lowering your expenditures. You save money not just on the abrasive itself, but also on its management & disposal.
The grit blasting room wall panels are fabricated from MS Sheet. Each wall panel is individually replaceable & is bolted concurrently on assembly. Wall panels & ceiling panels are fabricated from wide steel sheets respectively. Suitable supporting structure of angle/channel equipped for strength & rigidity of blast room. The door [in two leaves] hinge type shall be delivered on one side of the blast room. The door shall be fabricated from an MS sheet suitably engineered & constructed for rigidity. Each leaf of door shall be furnished with a concept window of Size 200 mm x 200 mm. 3 mm thick rubber hanging sheets on inside walls & inside exterior of door are pasted with 3 mm wide rubber sheets for protection against abrasion. The rubber lining is of natural rubber.
Industrial blasting gun bodies of suction blast cabinet systems vary betwixt 12-38 SCFM. The pressure blast cabinet systems vary betwixt 12-68 scfm & the pressure blast room systems utilize until 254 scfm. Industrial air compressors produce around 4.5 SCFM per horsepower (HP). Blasting cabinets mandate 3-15 hp compressors per nozzle & blast rooms could operate until 53 HP per man & nozzle.
Air consumption & media delivery rates are significantly greater in blast rooms & outdoor blasting systems than in pressure blasting cabinets. The air collection hose ID, the media blast hose ID, the nozzle ID, the pressure pot, & the pot piping are all substantially bigger in blast rooms than in cabinet systems. The increased productivity is also owing to the nozzle's greater length from the jobpiece in blast chambers, whichever results in a bigger blast pattern.
Automated enclosures & grit blast rooms are designed to handle diverse sizes & shapes of elements. The containment systems are developed to manage & contain blast material & elements inside the enclosures. The enclosure systems engage gravity to execute the blasted material to a collection area, from which it is enchanted to reclamation system. Blast systems might have cheap or expensive containment systems. Matching the appropriate containment system to an application is critical.
Steel blast media is known in both round/spherical shapes (conditioned cut wire & cast shot) & angular steel grit. Steel abrasives are extremely robust, making them a preferred option in blast rooms & automated wheel applications. The hardness ranges betwixt 40 & 65 Rockwell. Conditioned cut wire (rounded) is the preferred shot peening material over cast shot, which creates an adverse angular breakdown during blasting. Steel shot & grit are frequently employed to provide anchorperson designs and nice finishing. Steel shot may be blasted under extremely elevated pressures of until 110 PSI. The media cycle lives betwixt 80 & 100 times throughout the blast cycle.
A dust collector is an important element of every grit blast room. It offers ventilation within the room & filters pollutants from exhaust air. The dust collector must be carefully chosen to fit size of grit blast room in order to preserve visibility & the requisite air velocity in the room. Generally, the dust collector grows in proportion to grit blasting room's cross-section.
There are five major elements in an arrangement blasting room.
We are one of the best grit blasting room manufacturer and also a supplier of grit blast rooms in India. We offer all types of grit blasting machines, grit blasting cabinets, grit blasting rooms, automatic grit blasting machines, sand blasting machines, shot blasting machines, pressure blasting cabinets, suction blasting cabinets, etc.