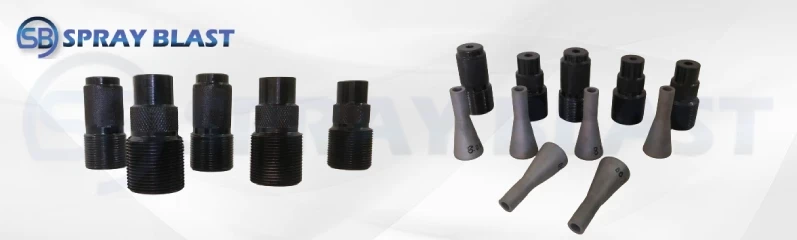
Abrasive Blasting Nozzle
An abrasive blasting nozzle is equipment that attaches to blast hoses & directs abrasive media onto the area existing treated. Every kind of blast nozzle on the market is created for a certain usefulness, whichever is why they vary in shape, size, & material. Surface preparation professionals prefer to have a scope of nozzles on hand for additional tasks since individual kinds of abrasive blasting nozzles include advantages & limitations. Spray Blast is a prominent manufacturer of blast nozzles & further flow control equipment for contractor abrasive blasting machines in configuration sector, as well as suction & pressure blast cabinets in the manufacturing industry. Spray Blast delivers tungsten carbide, BP200 SiAlON, boron carbide, & aluminum oxide nozzles & inserts in hundreds of sizes & designs to achieve your every demand.
When selecting a nozzle, there is a proportion to be fulfilled, which begins accompanied by your air compressor. Once you comprehend how your compressor's size impacts exhibition capacity, you'll want to consider nozzle size. Too big a hole will result in insufficient pressure to blast productively.
Straight bore & venturi are the two major abrasive sand blasting nozzle forms, each accompanied by its own size & pattern variants. Finally, examine material of an abrasive blasting nozzle. Particularly, substance utilized to line the hole. Three most essential considerations for determining best nozzle bore material are durability, consequence resistance, & pricing.
Types of Abrasive Blasting Nozzle
According To Shape
An abrasive blasting nozzle's bore shape dictates the blast pattern demanded for the application.
- Straight bore nozzles deliver an inflexible blast pattern, assembling them appropriate for blasting tiny areas.
- Venturi bore nozzles deliver a broad blast pattern & enhance particle velocity, whichever boosts productiveness when blasting bigger areas.
Venturi-shaped nozzles progressively taper outward from aperture to end of an abrasive blasting nozzle. This progressive exit increase permits air & media to mingle enclosed by the nozzle, enabling them to expand equally before exiting it. A venturi nozzle offers heightened peening intensity & cleaning capacities in a broad pattern. The venturi nozzle's implementation is specified by the proper ratio of length to orifice size, as well as the entrance & exit tapers. This design offers a huge blast pattern, resulting in greatest cleaning acceleration.
For more info about the sand basting machine visit our website.
As nozzles deteriorate from repeated disclosure to elevated velocity media, more air & media may travel via the orifice. The improved area enclosed by the nozzle operates more air volume, improving directive on the compressed air supply. If air volume can't maintain accompanied by the increasing discharge, pressure at the nozzle will decrease. Accompanied by less pressure, peening intensity & production diminish, & efficiency decrease. A suitable rule of thumb for maintaining consistent heightened output is to substitute the nozzle when the orifice wears to the following bigger size.
For vapor abrasive blasting, the most often used nozzle orifice widths range from 3/8" inner diameter to 3/4", with 1/16" increments. A 3/8" nozzle can create an efficacious blast pressure utilizing a 5.32 m3/min (185 CFM) air compressor. A 1/2" nozzle is adequate to deliver a compelling blast pressure accompanied by a 10.62 m3/min (375 CFM) compressor.
It is vital to remember certain doubling the diameter of the orifice quadruples its size as well as the magnitude of air & abrasive media certain may travel via the nozzle. To discover your most efficacious nozzle, first, specify the nozzle pressure in bar (PSI) you ought to maintain for effective blasting & volume of air your general compressor can deliver per minute (m3/min (CFM)), then operate to find nozzle orifice size certain encounters those parameters.
To maximize productiveness, establish the nozzle bore size hanging on the mandated blast pressure as well as unrestricted air pressure & flow rate. For example, suppose you're running a 375 cfm compressor at 80% capacity. In expansion to blast cleaning nozzle, the compressor delivers air to an air helmet & different elements like air motors & pneumatic controls, exiting 250 cfm for abrasive blasting nozzle. 250 cfm is acceptable for a 7/16" nozzle running at 100 psi. A bigger nozzle, such as a stale 7/16" nozzle, will demand more airflow to sustain 100 psi. This increased flow need will either overload your compressor & reduce production. Choosing a nozzle accompanied by a bore narrower than your compressor's capacity will result in less than greatest system productiveness.
According To Material
Nozzle material selection is selected by abrasive employed, the frequency with whichever you blast, size of task, & directions of project site. The subsequent are available application rules for distinct materials.
Aluminum Oxide Nozzle
Aluminum Oxide "Alumina" (Ceramic) Nozzles deliver a long usefulness life at a lesser cost than different materials. They are an outstanding alternative for low-usage applications wherever unit pricing is a significant consideration & nozzle life is less critical.
Tungsten Carbide Nozzle
Tungsten carbide nozzles deliver extended life & economic value when harsh handling is unavoidable when mineral & coal slag abrasives are utilized. Not all tungsten carbide nozzles are the same; nozzles are constructed of high-quality wear-resistant material & are built to last.
BP200 SiAION Nozzle
BP200 SiAION Nozzles deliver a usefulness life & durability comparative to tungsten carbide, though are roughly half weight. BP200 SiAION nozzles are a good alternative for operators who work long hours & desire a lightweight nozzle.
Boron Carbide Nozzle
Boron carbide nozzles last a long time when employed accompanied by right air & abrasives. Boron carbide is appropriate for harsh abrasives like aluminum oxide & some mineral entireties when rough handling is evaded. Boron carbide often outwears tungsten carbide by five to ten times.
Composite Carbide Nozzle
Composite carbide nozzles last even longer than boron carbide nozzles. This nozzle material is suited for applications that need harsh abrasives like aluminum oxide & silicon carbide. Particular angle nozzles, industrial gun inserts for famous models, etching nozzles, & pencil blast nozzles are just a infrequent of the specialty nozzles available today.
Abrasive Blasting Nozzle Manufacturer in India
Spray Blast is the leading abrasive blasting nozzle manufacturer in India and also the supplier of abrasive blasting nozzles all over the world. We provide all types of abrasive blasting nozzle such as tungsten carbide nozzle, silicon carbide nozzle, aluminum oxide nozzle, boron carbide nozzle, and more. To buy as per your requirement all types of abrasive blasting machines like sand blasting machines, grit blasting machine, sand blasting cabinets, benchtop sand blasting cabinets, and abrasive blasting rooms, contact us.